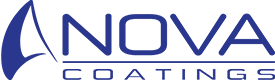
A Brief History of Early Sandblasting
Sandblasting has a longer history than you might expect. The absolute furthest it can be traced back is 1870, when Benjamin Tilghman invented a machine for paint and rust removal.
Further progress was made by Thomas Pangborn by adding compressed air in 1904; and the innovation of the use of enclosure was built in 1918. The enclosure contained a clear screen for sandblasters to surround the worksite and prevent dust from hitting workers’ faces.
By the 1930s, sandblasting was well-known in manufacturing fields. A change in attitude about sandblasting occurred when the U.S. Navy needed more efficient ways to prolong the service life of their coating systems as simple scraping and sanding did not bring about satisfactory results, the Navy attempted sandblasting. Upon completion, the Navy realized that sandblasting was a necessary process to achieve good adhesion and lasting performance of the coating system.
This successful project set the foundation for the protective coating industry and numerous future success stories.
Sandblasting has evolved significantly, becoming safer and more efficient.
Sandblasting or abrasive blasting is an extremely fast and effective dry abrasive blasting or wet abrasive blasting method where pressurised air is used to blast sand against a surface to thoroughly remove previously painted coating, mill scale and corrosion from steel.
Almost instantly, abrasive sandblasting restores surfaces to look new again and creates a perfect surface profile for paint adhesion and long lasting results.
While the use of sand gives abrasive sand blasting its name, garnet is the most common abrasive material. Other blast material types can also be used.
Nova protective Coatings has extensive experience in industrial protective coatings and preservation of client assets.
If you’re looking for abrasive blasting contractors, look no further as our abrasive blasting team have extensive knowledge and skill when it comes to abrasive blasting. We continue to invest significantly in state-of-the-art equipment and advanced training of our personnel, allowing us to provide efficient, cost-effective and innovative solutions with optimum results and timely completion of projects in even the most sensitive environments.
For more information about
Please contact our Operations Manager or Projects Supervisor